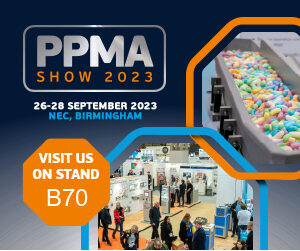
See our high-speed Intelligent Motion Feeder with high-integrity seal Flow Wrapper
Visit stand B70 Hall 5 at PPMA 2023 26 – 28 September 2023 and witness our latest high-speed pressure-less IMF Intelligent Motion Feeder seamlessly feeding products into the FT120 Flow Wrapper with precision and speed redefining packaging efficiency and flexibility.
The FT120 Flow Wrapper will reveal an exciting enhancement with the integration of a cutting-edge sealing module. This innovative addition is designed to seal horizontally elevating standards of high integrity sealing as well as enhancing overall performance when working with more challenging and eco-friendly recyclable packaging films.
Be part of the future of packaging; we can’t wait to show you the next level of innovation!
The IMF Intelligent Motion Feeder, with Integrated Layer Collator, features the Bradman Lake’s latest product handling technology, using Rockwell Automation’s small frame iTRAK intelligent track system.
The IMF will automatically feed products into an FT120 Flow Wrapper that will incorporate the new sealing module. The IMF incorporates new servo-driven linear guided carriers that accept a randomly spaced stream of products, which are positioned and transferred into the infeed of the flow wrapper (or other packaging machines), negating the need for traditional feeders. This provides excellent access for the end user, the option of constant or indexing motion on the same machine and greater flexibility in handling a wide range of products and collations.
IMF Intelligent Motion Feeder, with Integrated Layer Collator Features:
High speed, up to 600 products per minute.
Greater tolerance to product positioning, for higher packaging efficiency.
Rapid changeover, no tools required, which increases productivity.
Easy cleaning with no mechanisms below the product line for greater sanitation.
Small footprint, new frame style, and full-height doors for ease of access.
Common control architecture.
FT120 Flow Wrapper Features:
Operates at the highest level of efficiency and seal integrity, even for challenging heat-seal applications.
New and improved ‘backward compatible’ flow wrap sealing technologies. Simple conversion parts or modular replacements can enable the flow wrapper to run recyclable, biodegradable, paper and single substrate mono materials.
Robust end crimp sealing module that provides hot or cold seal options.
Quick changeover takes less than 15 minutes and requires only a single operator. It is simple to operate and maintain as well as being able to accommodate a wide range of product sizes.
Soft Jaw. Unique to Bradman Lake, it prevents misplaced products from jamming in the end seal jaws.
Reel to Reel Splicing. Automatic splicing is a standard feature on a system. A manual splice is also available for stand-alone machines.
Automatic Web Tracking. Maintains position of wrapping material presentation from the reel, providing increased efficiency and productivity whilst keeping material width to a minimum.
Discharge Top Control. It provides a consistent transfer onto the discharge conveyor, therefore, ensuring a regular pitch between products when interfacing with downstream equipment.
No Gap No Crimp. If no gap is detected between products on the infeed, the end seal jaws will not come together, and a long bag is formed that is rejected on the machine infeed. The machine does not stop production.
No Product No Bag. If no product is detected in the machine pitch, the end seal jaws simply wait for the next product. No empty pack is produced, so there is no wastage and the machine continues to run.
High Speed. Machine versions capable of wrapping speeds up to 1200 packs per minute are available.
Visitors to the booth will also have an opportunity to see a curated video collection. These videos will illustrate how the packaging equipment on display seamlessly integrates with Bradman Lake’s downstream equipment that includes cartoners, case packers, shrink wrappers and palletisers creating a flawless end-to-end process. This reaffirms Bradman Lake as the ultimate one-stop shop for packaging solutions – where innovation meets integration.
Features and benefits for all Bradman Lake’s equipment:
Bradman Lake packaging equipment sets the benchmark for primary, secondary and tertiary packaging. Equipment can be supplied as a ‘stand-alone’ machine for low speed, hand-fed applications, or as a fully automatic system to meet the demands of the most sophisticated hi-tech processing and packaging lines. They have become the machines of choice for many multinational manufacturers operating in the bakery & biscuit, chocolate & confectionery, dry foods, chilled & frozen foods, pharmaceutical, and healthcare industries.
Experience. Bradman Lake has a large installed base; our customers benefit from over 75 years of knowledge in designing and building packaging equipment. Bradman Lake is an established brand with a high reputation for machine reliability and value for money worldwide. Its position as an innovative, progressive and forward-thinking global supplier of packaging solutions derives from vast industry experience, a consultative, customer driven approach, delivering commercially viable solutions with strong project management and a commendable health and safety record.
All Bradman Lake products are the result of thoroughgoing research and development and are developed from an undertaking that every project, no matter how small or technically challenging, will be a custom solution to meet exact customer requirements. This responsive, solutions-based approach has helped establish Bradman Lake as a leading global provider of future-proof packaging technology.
Flexibility, “Future Proof” Principal. The ergonomic modular design provides the ultimate flexibility to handle a wide range of products, carton formats and sizes that can be rapidly adapted to specific requirements enabling our customers to easily meet the demands of the fast-changing markets at any time in the future.
Sustainability. Environmental sustainability is an important focus for Bradman Lake, both in machine development and business operation. As well as promoting recycled packaging, it seeks to minimise packaging material waste through various equipment features. Ergonomic equipment design enables concurrent task completion in one compact frame, reducing spatial requirements, lowering energy and air consumption while ensuring no harmful emissions are produced.
Bradman Lake is proud to communicate its machinery helps to remove many millions of single use plastic trays year on year!
Safety and Hygiene. Robust and well-built to the latest safety and hygiene standards. Upgradable machine construction to handle wash-down applications that are required in the food and healthcare industries. Machine guarding has been designed to provide operator safety, maximum visibility of operation and excellent machine access.
From Process to Pallet. Bradman Lake provides true, single-source turnkey systems, with project management from initial concept to site acceptance and beyond. The benefits to customers include commonality of engineering standards and parts; a single servo motor size, common wiring patterns and identical HMI look-and-feel all contribute to ease of use and operation; a single point of contact for procurement; project manager and aftermarket; FAT for full system occurs in single location and systems are fully integrated and tested prior to delivery resulting in expedited start up.
Intuitive HMIs and a common control platform offer customers an easier method of extracting information from a single source, as well as seamless exchange of data upstream and downstream. A single network infrastructure offers unprecedented levels of visibility, flexibility and scalability to respond to market opportunities and operational threats.
Initial Capital Savings. The core competence of the equipment is its unique capability for seamless future integration with other Bradman Lake innovative equipment to achieve full automation and yet retain initial capital savings.
Smart Layout. Compact footprint which is available in several orientations to suit plant layout and incorporates narrow integral electrical cabinets with easy access. All machines are designed with minimum frame sizes and easy-access guard design.
Customer Service: Backed by readily available and award-winning customer support, commercial commitment, resources, and spare parts delivery.
About Bradman Lake
Established in 1948, Bradman Lake provides innovative packaging solutions to an international client base. The company is a leading designer and manufacturer of packing machinery and turnkey systems to the bakery & biscuit, chocolate & confectionery, dry foods, chilled and frozen foods, consumer, pharmaceutical and healthcare sectors. In 2022 the company was awarded the prestigious Queens Award for Enterprise. Bradman Lake’s manufacturing plants are located at Beccles and Bristol in the UK and Rock Hill, SC, in the United States. Bradman Lake is a wholly owned subsidiary of the multi-disciplined UK engineering and manufacturing group, Langley Holdings plc.