
Chocolate and confectionery
We have a wealth of experience supplying packaging machinery to the world’s chocolate and confectionery industries.
Our knowledge in the gentle handling of all types of chocolate and confectionery products is second to none. From single ‘stand-alone’ machines to complete high-speed packaging systems, the Bradman Lake Group offers a comprehensive range of product storage and distribution, orientation and collating, flow wrapping and roll wrapping machines, robotic loading, cartoning, wraparound tray and case packing systems.
Bradman Lake's Packaging Systems For Chocolate and Confectionery
Bradman Lake’s integrated packaging technologies deliver innovative, turnkey solutions to provide increased system performance, higher speeds and efficiency, reduction of waste in both product and wrapping materials as well as decreased changeover times and reduced labour costs. This fully automatic bar packaging system illustrates the Bradman Lake ‘single source solution’ capability. Additional features which can be easily incorporated, include full line management control and consumer protection packages.
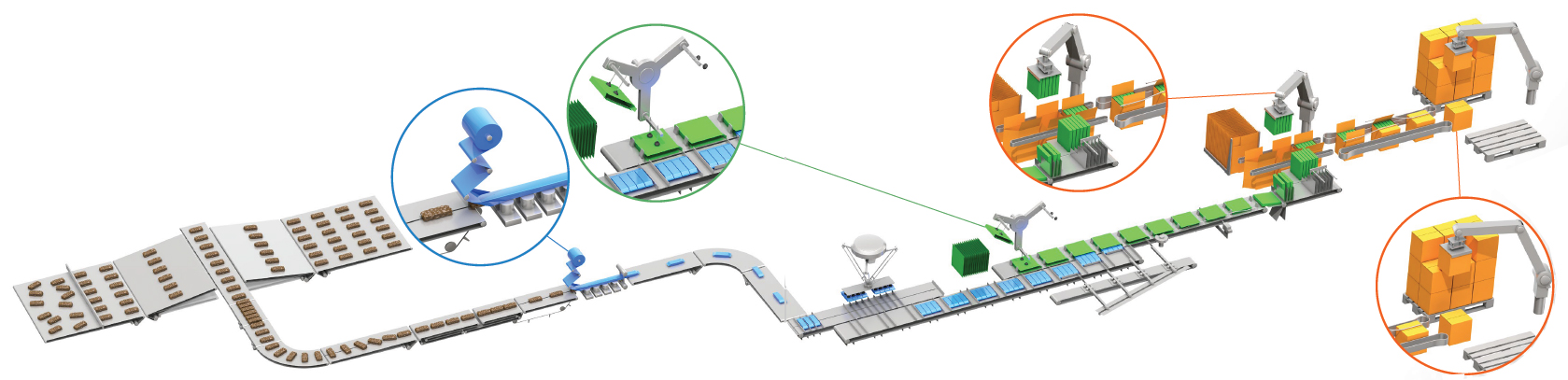
The bar packing system includes:
Primary Packaging: Row conditioning, row feed station, product orientation, smart belt pressureless, phase feeding and flow wrapping.
Secondary Packaging: Race track flow wrap collating, robotic picking and placing and end load cartoning.
Tertiary Packaging: Race track carton collating, case erection, robotic case loading, case closing, robotic palletising.
Other configurations are available based on the customers’ requirements.
The packing system will take product from the oven and cooling tunnel, through each packaging process and deliver a collation of cases onto a pallet ready for shipping. Product is orientated, then a pressureless phase feeding system collates the product to be wrapped using either hot or cold seal material to provide the level of sealing and protection required. Cartons are formed using either a lock or hot glue system and the flow wrapped product is robotically loaded in the required ‘layer and collation’ format. The lids of the cartons are then glued closed using Bradman Lake’s unique ‘flexible carton control’ technology and presented to a collation unit that will form the final collocation to be robotically loaded into cases and then sealed using hot glue or tape. Sealed cases are robotically loaded on a pallet, with slip sheets between them for extra protection.
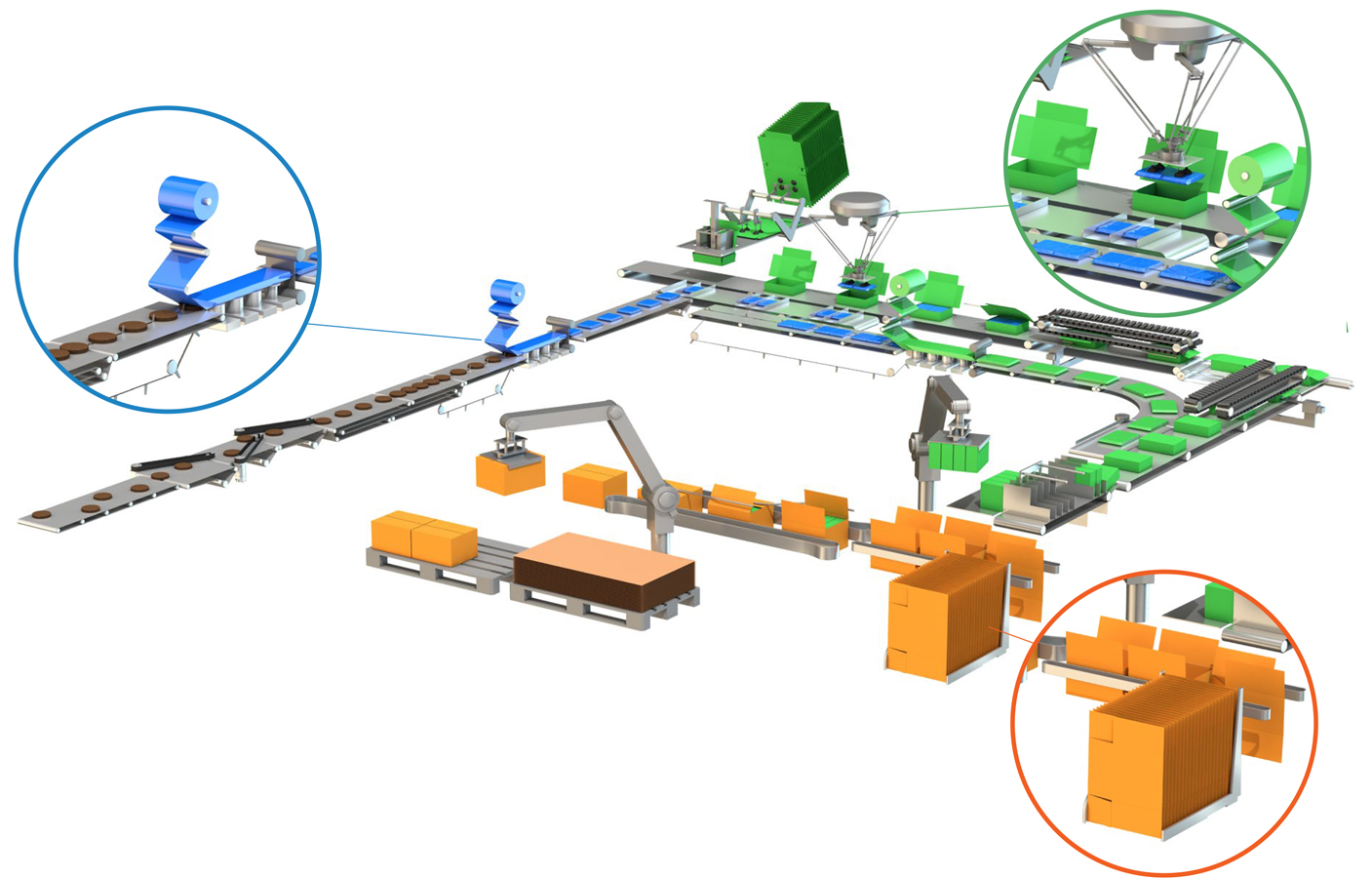
The enrobed biscuit and cookie packing system includes:
Primary Packaging: Product orientation, smart belt and flow wrapping.
Secondary Packaging: Racetrack collating, carton erection, robotic pick and
place loading, carton closing and multipack flow wrapping.
Tertiary Packaging: Race track carton collating, case erection, robotic case loading, case closing, robotic palletising, and slip-sheet insertion.
Other configurations are available based on the customers’ requirements.
It is a simple and versatile system designed to quickly and effectively package small round, square, and rectangular confectionery items. It uses a rolling head belt wrapping principle to ensure consistent wrapping and secure product containment. Packs can be produced with either single overall wraps or overall wraps with outer label. Cartons are formed using either a lock or hot glue system and the roll wrapped product is robotically loaded in the required ‘layer and collation’ format. The lids of the cartons are then glued closed using Bradman Lake’s unique ‘flexible carton control’ technology and presented to a collation unit that will form the final product collation to be sealed in a shrink wrap material.
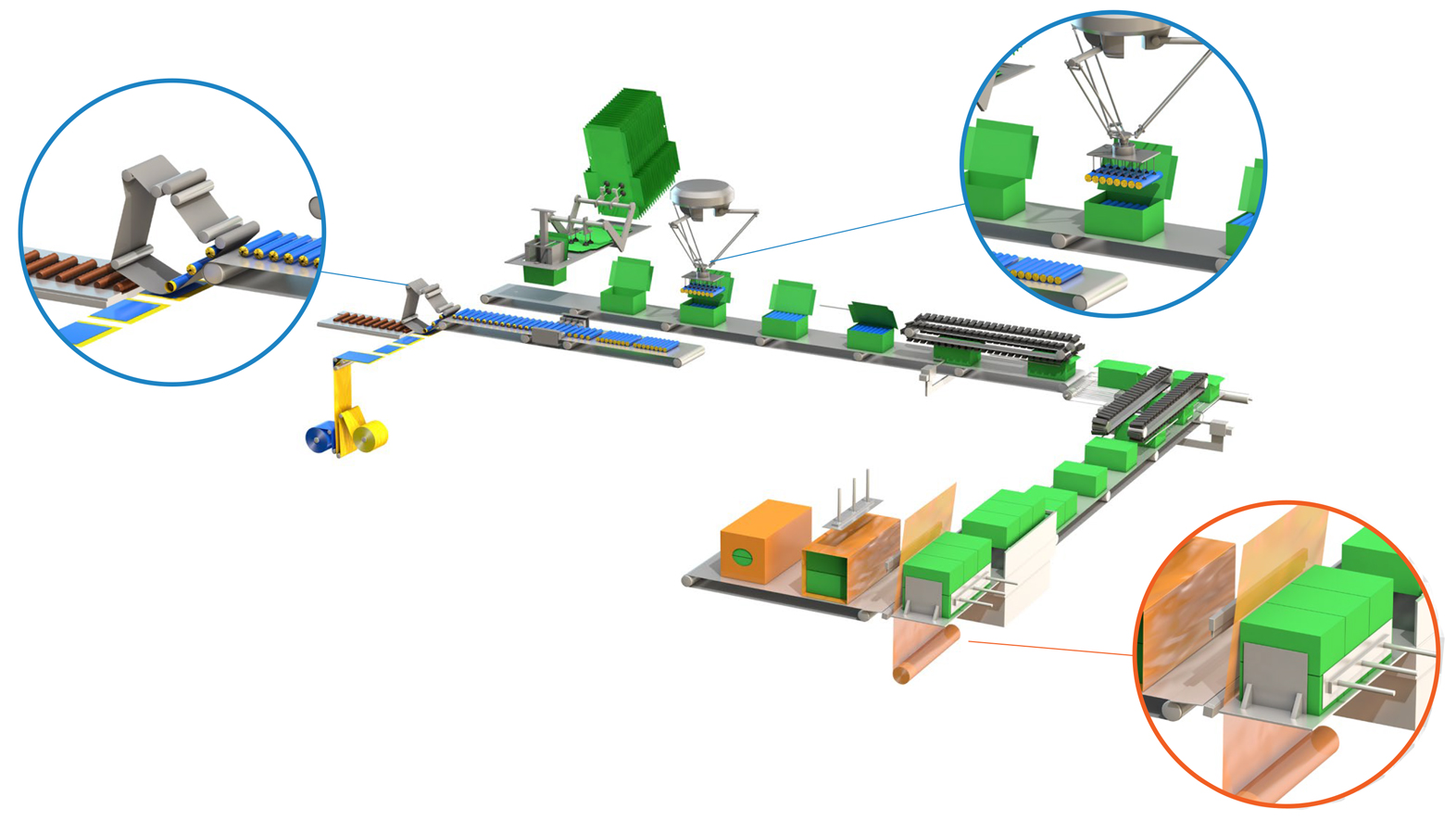
The roll wrapping packing system includes:
Primary Packaging: Roll wrapping.
Secondary Packaging: Race track collating, carton erection, robotic pick and
place loading, and carton closing.
Tertiary Packaging: Collating and shrink wrapping.
Other configurations are available based on the customers’ requirements.
Bradman Lake on-edge packing systems utilise proven technology. The collations are fully supported through the flow wrapping process. To minimise product damage and maintain collation form, Race Track technology collates the required pack count to end-load into the carton. The wraparound case packer allows for material savings via flat blanks and skeletal case formats.
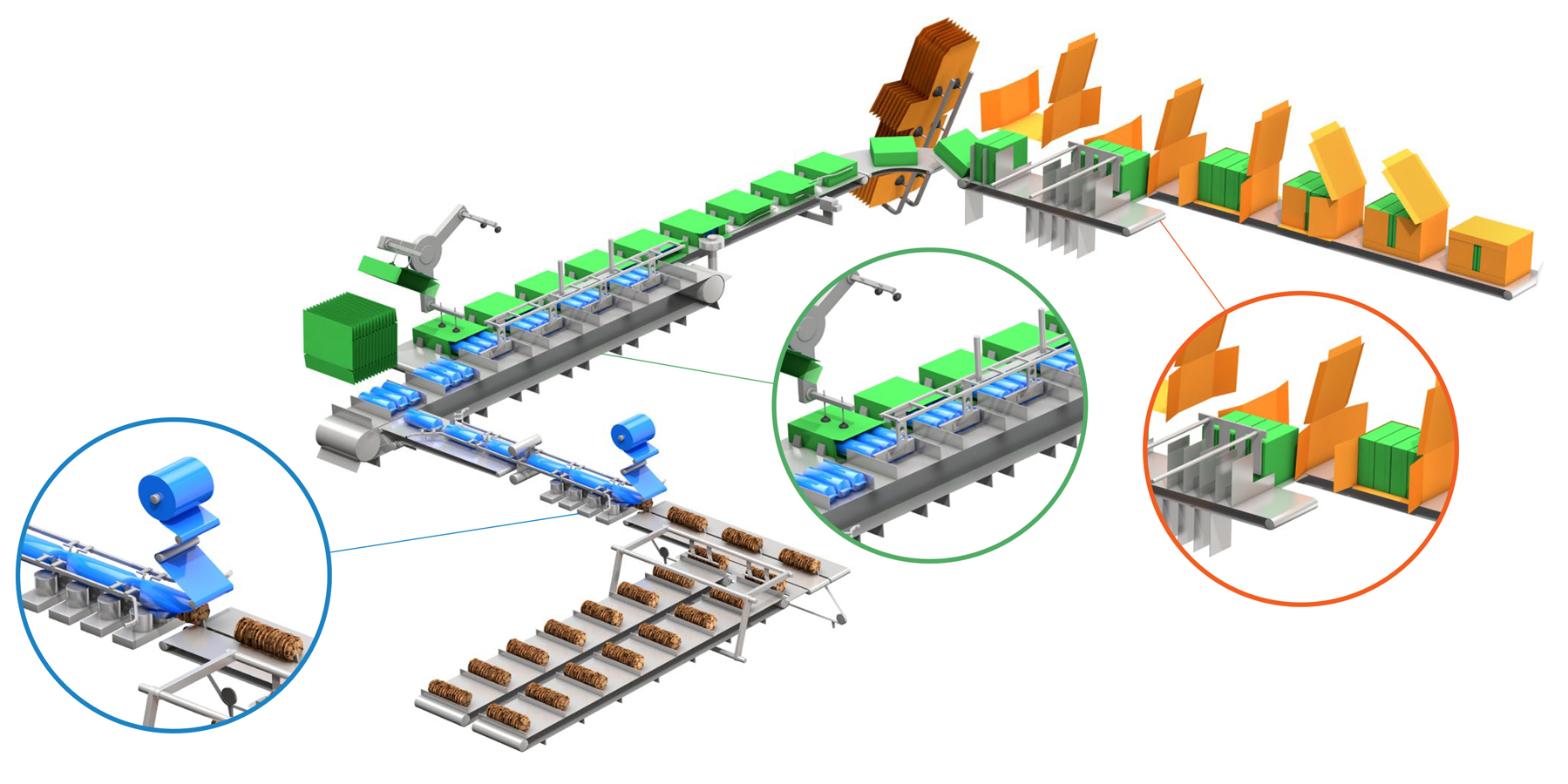
The on-edge packing system includes:
Primary Packaging: Product orientating, collating and ‘on edge’ flow wrapping.
Secondary Packaging: Race track collating and end load cartoning.
Tertiary Packaging: Race track carton orientation and collation and case packing.
Other configurations are available based on the customers’ requirements.
Designed to accept product from two primary sources. Uses a dual DRT system, feeding product from either direction to a central loading station.
Eliminates the need to merge products prior to carton loading. Cartons are formed using either a lock or hot glue system.
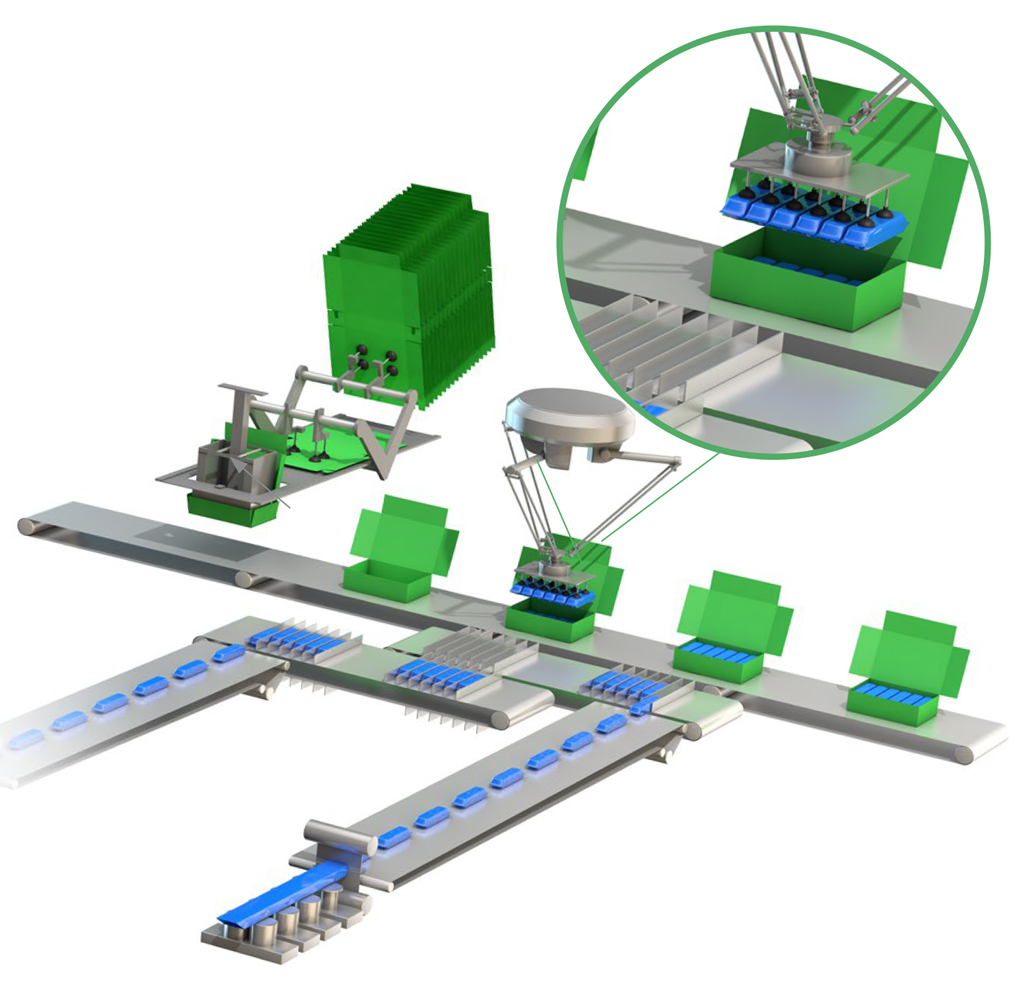
The on-edge packing system includes:
Secondary Packaging: Carton erecting, race track collating and top load cartoning.
Other configurations are available based on the customers’ requirements.
Get in touch
Contact us today for a free consultation, quote, and to request our brochure specifically designed for the chocolate and confectionery industry.